Programm
Wissensforum Zerspanung 2024
26. November 2024
16:00 - 17:30
Werksführung durch die Fertigung beim Druckmaschinenhersteller

Freuen Sie sich auf dieses besondere Highlight der Veranstaltung: Erhalten Sie während der exklusiven Werksführung einzigartige Einblicke in modernste Fertigungsprozesse und erleben Sie hautnah, wie Innovation und Präzision in der Produktion zusammenkommen.
Hinweis: Limitierte Teilnehmeranzahl von max. 60 Personen (2 Führungen à 30 Personen)
ab 19:00
Netzwerkabend am Vorabend
Wir laden Sie herzlich ein, den Abend des 26. November 2024 mit uns in der REISERS Genussmanufaktur zu verbringen! Stimmen Sie sich schon hier auf die Veranstaltung ein! Kommen Sie miteinander ins Gespräch und tauschen Sie sich über aktuelle Themen der Zerspanungsbranche aus. Genießen Sie intensives Networking in stimmungsvoller Atmosphäre!
27. November 2024
08:30 - 09:00
Check-in & Welcome coffee
Willkommensfrühstück und Besuch der Ausstellung
09:00 - 09:10
Begrüßung sowie Vorstellung der Agenda & Ziele
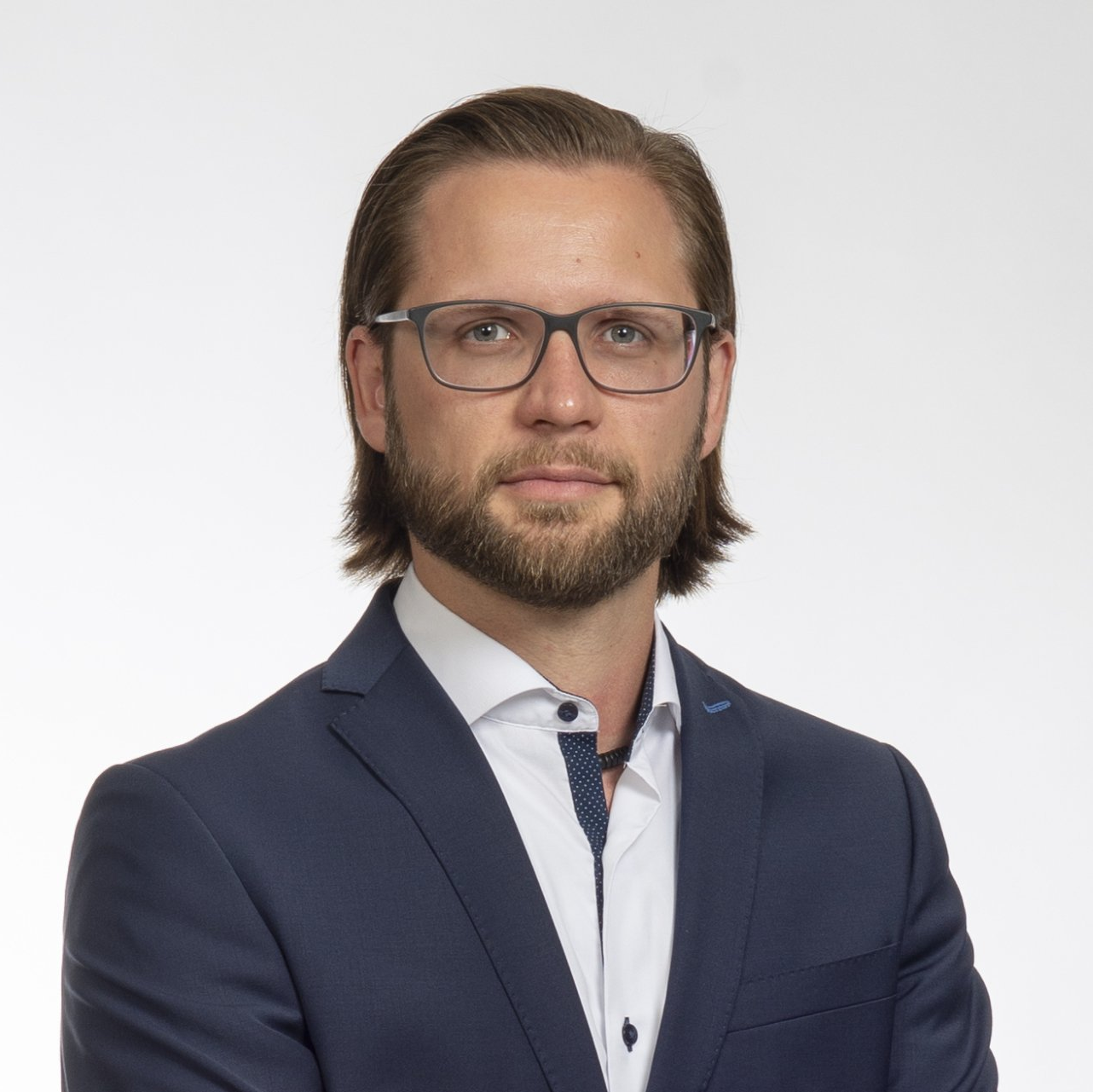
Chefredakteur MaschinenMarkt | Vogel Communications Group
09:10 - 09:40
Keynote-Vortrag
Closed-loop manufacturing – Bidirektionale Datendurchgängigkeit vom Engineering zur Maschine
mehr zum Vortrag erfahren
Im Vortrag werden die aktuellen Herausforderungen von Fachkräftemangel, steigenden Energiekosten bei gleichzeitiger Erhöhung der Komplexität von Bauteilen, geringeren Losgrößen und reduzierten Lieferzeiten dargestellt. DMG MORI begegnet diesen Veränderungsfeldern mit Machining Transformation (MX) und fortschrittlichen Fertigungslösungen. Die vier Säulen der Machining Transformation (MX) sind Prozessintegration, Automation, Grüne Transformation (GX) und die Digitale Transformation (DX). Dabei bildet die bidirektionale Datendurchgängigkeit mit digitalen Zwillingen einen Baustein, um die aktuellen Herausforderungen zu meistern.
Es wird gezeigt, wie durch closed-loop Abläufe vom Engineering bis zur Maschine mit der neusten Steuerungsgeneration von Siemens – SINUMERIK ONE auf den DMG MORI-Bearbeitungszentren die Energieeffizienz erhöht wird, bei gleichzeitiger Reduzierung der Einfahrzeit durch kollisionsfreie Bearbeitung. Die Rüstzeit wird reduziert und die Flexibilität durch die Betrachtung des Auftragsprozesses erhöht. Hierbei werden die aktuellen Situationen in der Fertigung im Auftragsprozess berücksichtigt, welche den gesamten Shopfloor mit den angrenzten Dienstleistungen, wie Werkzeugbereitstellung, etc. einschließen.
Um die Prozessketten zu schließen (closed loop) und daraus kontinuierliche Verbesserungen zu erzielen, werden die gewonnen Daten aus der Maschine in die Planungsebenen zurückgeführt.
Die Partnerschaft zwischen Siemens und DMG MORI bildet die Basis, um durch tiefe Integrationen zwischen der Planungswelt und der Werkzeugmaschine den Wertschöpfungsprozess dementsprechend stetig zu erhöhen.
Der kontinuierliche Verbesserungsprozess aus technischer und kommerzieller Sicht bildet die Basis um die Fertigung flexibel mit kleiner Losgröße, niedrigen Kosten stetig zu optimieren, um die Einzelteilfertigung zu Kosten der Großserie herstellen zu können.
Der Vortrag veranschaulicht die Effekte in Prozessketten und kurzen Videosequenzen und erklärt, wie die Effekte erzielt werden, um den Produktionsstandort Deutschland bei schwierigen Bedingungen weiterhin attraktiv zu halten.
09:40 - 10:00
Präzises Außenrundschleifen: Herausforderungen und Lösungen bei hochharten Werkstoffen
mehr zum Vortrag erfahren
Ziel dieses Vortrags ist es, die Mechanismen des Materialabtrags sowohl beim konventionellen Schleifen als auch beim lasergestützten Schleifen von hochharten Werkstoffen zu erläutern. Es wird versucht, Ursache-Wirkungs-Beziehungen zwischen den Schleifscheibenspezifikationen, den Schleifparametern, der Laserstrukturierung, der Materialabtragsrate und der Werkstückqualität herzustellen. Die gewonnenen Erkenntnisse sollen dazu beitragen, die Effizienz und Leistung bei der Bearbeitung hochharter Werkstoffe deutlich zu verbessern.
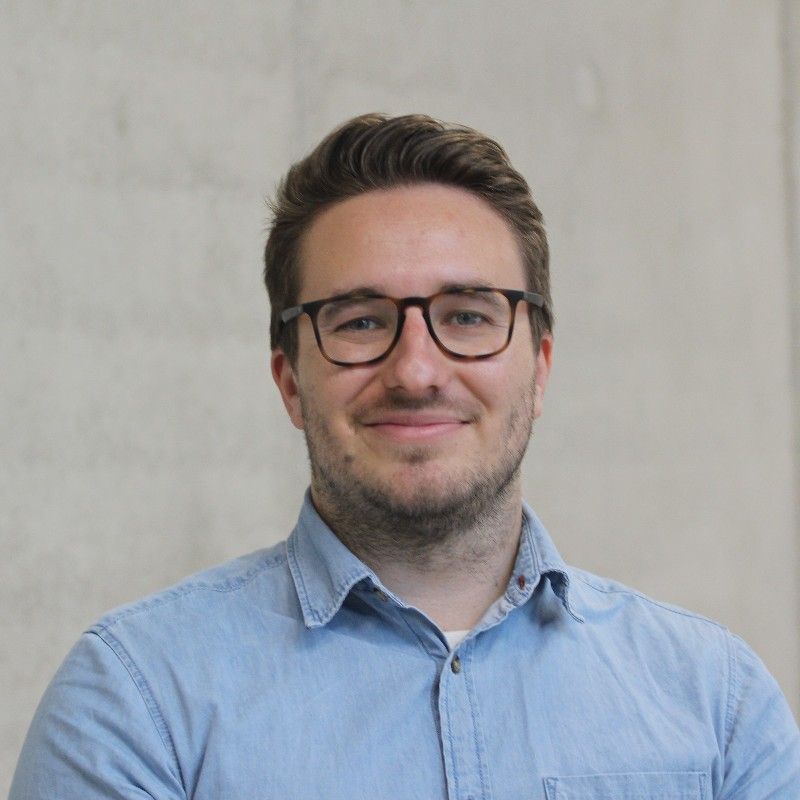
Hochschule Furtwangen
10:00 - 10:20
Ultraschallunterstützung zur Steigerung von Effizienz und Präzision in der Hochpräzisions-Fräsbearbeitung
mehr zum Vortrag erfahren
Die Nutzung von ultraschallunterstützten Systemen stellt eine der vielversprechendsten technologischen Weiterentwicklungen bestehender spanender Bearbeitungsprozesse dar. Im Falle von Fräsprozessen können durch die Überlagerung der Werkzeugrotation mit einer hochfrequenten Schwingung bei der Bearbeitung anspruchsvoller Werkstoffe erhebliche Vorteile erzielt werden. Dazu zählen beispielsweise eine signifikante Reduktion der auftretenden Prozesskräfte - besonders relevant für filigrane Bauteile aus spröden Werkstoffen - und die Verringerung des Werkzeugverschleißes infolge veränderter Reibbedingungen in der Kontaktzone des Werkzeuges, was wiederum eine Senkung der Zerspantemperatur bedingt. Ein weiterer Vorteil liegt in der Steigerung des Zeitspanvolumens bei der Bearbeitung spröder Werkstoffe durch die Induktion oberflächennaher Mikrozerrüttungen.
Im Rahmen eines Kooperationsprojektes wurde ein innovatives Maschinensystem auf Basis der Hochpräzisionsfräsmaschine MP7/5 des Herstellers EXERON GMBH, Oberdorf, entwickelt, in welchem ein neuartiges Konzept zur Energieübertragung realisiert werden konnte. Die durch das optimierte System übertragene elektrische Energie wird mithilfe eines in den Werkzeughalter integrierten Ultraschallwandlers in mechanische Schwingungen umgewandelt. Das Ultraschallsystem wurde von der SON-X GMBH, Aachen, entwickelt und umgesetzt. Das Maschinensystem adressiert aufgrund der hohen Dynamik und Präzision seiner Linearachsen in Verbindung mit der speziell konstruierten Hochdrehzahlspindel HSC-Anwendungsfälle aus den Bereichen der Medizintechnik, des Werkzeug- und Formenbaues sowie der Fertigung von Konsum- und Luxusgütern.
Im Rahmen von Zerspanversuchen konnte die Funktionalität des Systems anhand von Graphitwerkstoffen verifiziert werden. Es konnte gezeigt werden, dass mithilfe des entwickelten Maschinensystems der Verschleiß der genutzten CVD-beschichteten Werkzeuge sowie die entstehenden Zerspankräfte signifikant reduziert werden konnten.
TU Berlin
10:20 - 10:40
Die neue Revolverschnittstelle PTI, ihre Leistungsmerkmale, die Normung und aktuelle Anwendungen
mehr zum Vortrag erfahren
Ende der 80er Jahre begründete das Werkzeugmaschinenlabor ( der RWTH Aachen ein Themengebiet, das es in der Form bis dahin noch nicht gegeben hatte: die Schnittstelle zwischen Maschine und Werkzeug. Ein erstes Entwicklungsergebnis war die HSK Schnittstelle, die Mitte der 90er Jahre international genormt wurde. Während die HSK Normen im Wesentlichen Schnittstellen für den rotierenden Einsatz in Spindeln für Bearbeitungszentren beschreiben, fehlen seitens der Drehmaschinen, insbesondere Revolverdrehmaschinen, entsprechende Normen. Vor diesem Hintergrund entwickelte das WZL (C. Brecher) gemeinsam mit Vertretern der deutschen Werkzeug Maschinen Revolver und Spanntechnik Industrie in den letzten Jahren eine leistungsfähige und für die Normung geeignete Revolverschnittstelle. Es entstand die PTI Schnittstelle (Polygonal Turret Interface), deren internationale Normung im Juli dieses Jahres mit der Herausgabe der dreiteiligen Norm ISO 5686 1 ( 2 ( 3 (Kupplung für AGW) abgeschlossen wird. Für die überragende Leistungsfähigkeit des PTI, die in zahlreichen WZL Untersuchungen und bei ersten Anwendungen nachgewiesen wurde, ist neben der kegelig polygonalen Gestaltung vor allem das Spannsystem verantwortlich. Als weltweit führender Spanntechnikhersteller hat OTT JAKOB für alle drei PTI Nenngrößen ein manuelles Schnellwechselsystem entwickelt, die Serienproduktion begonnen und vermarktet PTI. In Deutschland hat PTI bei großen Endverbrauchern und Maschinenherstellern Interesse gefunden. Japanische Maschinenhersteller beschäftigen sich seit der JIMTOF 2022 mit PTI. In neuesten Projekten wird PTI erstmalig für das automatische Rüsten von Werkzeughaltern in Revolverdrehmaschinen eingesetzt.
10:40 - 11:00
Kaffee- & Snackpause
Möglichkeit zum Besuch der Ausstellung
11:00 - 11:20
Wirtschaftliche Zerspanung: Produktivität versus Nachhaltigkeit
mehr zum Vortrag erfahren
Die industrielle Produktion unterliegt bspw. aufgrund von gesetzlichen Vorgaben und steigenden Energie- und Rohstoffkosten zunehmend der Forderung nach einer effizienten Nutzung verschiedener Ressourcen. In diesem Zusammenhang rückt z. B. die in der industriellen Fertigung aufgewendete Energie im Lebenszyklus der eingesetzten Zerspanungswerkzeuge zunehmend in den Fokus. Um die Energieverbräuche in der Spanenden Fertigung ganzheitlich zu quantifizieren, wurde im Rahmen der durchgeführten Analysen neben dem Energieeinsatz im Zerspanprozess auch die Herstellungsroute von Hartmetallwerkzeugen exemplarisch charakterisiert. Auf Grundlage der ermittelten Leistungsaufnahmen wurde eine ganzheitliche Energiebetrachtung für die untersuchte Prozesskette erarbeitet.
In Zusammenhang mit der effizienten Nutzung von Energie und Ressourcen gilt Wasserstoff als einer der bedeutendsten Energieträger als Ersatz für fossile Brennstoffe. Die in der Wertschöpfungskette benötigte Anlagentechnik unterliegt jedoch aufgrund hoher Wasserstoff-Gasdrücke einer gesteigerten Anfälligkeit für Spannungsrisskorrosion, wodurch hohe Ansprüche an die Fertigung der verwendeten Komponenten hinsichtlich der Randzoneneigenschaften gestellt werden. Die Bearbeitbarkeit von zu diesem Zweck eingesetzten nichtrostenden CrNi-Stählen wie X2CrNiMo18-14-3 (1.4435) und X4CrNiMo16-5-1 (1.4418) stellt bspw. aufgrund starker Adhäsionsneigung und ungünstiger Spanform eine besondere Herausforderung dar. Um entsprechende Bedingungen für eine prozesssichere Bearbeitung bei gleichzeitig hoher Bauteilqualität zu ermöglichen, wurden experimentelle Untersuchungen zum Bohren und Gewinden durchgeführt. Dabei wurde neben dem Einsatzverhalten der Werkzeuge, die Bearbeitungsqualität analysiert. Insbesondere die Randzoneneigenschaften wurden im Rahmen von metallografischen Untersuchungen betrachtet und auf mögliche Bildung von Verformungs-Martensit untersucht.
Die im Rahmen dieses Vortrags vorgestellten Ergebnisse repräsentieren aktuelle Projekte des Arbeitskreises Zerspanung innovativer Stahlwerkstoffe. In enger Kooperation arbeiten hier die beteiligten Forschungsinstitute mit fertigenden Unternehmen sowie Werkzeug- und Stahlherstellern zu Herausforderungen im Bereich der Spanenden Bearbeitung von Stahlwerkstoffen zusammen. Konkret werden im Rahmen der halbjährlich stattfindenden Arbeitskreistreffen aktuelle Herausforderungen identifiziert, anschließend in Einsatzversuchen experimentell untersucht und gemeinschaftlich mit den beteiligten Partnern Lösungen erarbeitet.
11:20 - 11:40
Kombinieren von Bohren und Entgraten spart Zeit
mehr zum Vortrag erfahren
Bei steigenden Betriebskosten und gleichzeitig globaler Konkurrenz rücken Prozessoptimierungen immer mehr in den Fokus. Um die Effizienz zu steigern, gerade in der Fertigung von grossen Serien, spielt Zeit eine entscheidende Rolle. Wenn pro Arbeitsgang nur wenige Sekunden eingespart werden können, resultieren am Schluss der Serie Zeiteinsparungen von mehreren Stunden oder sogar Tagen. Doch wie kann in einem bereits optimierten Produktionsprozess weiter Zeit eingespart werden? Durch die Kombination von mehreren Operationen in einem Arbeitsgang! Dazu sind neue Werkzeugkonzepte nötig, die mehrere Arbeitsschritte vereinen.
In der Präsentation zeigen wir anhand von Bohr-Kombi-Werkzeugen auf, wie solche Kombinationen aussehen können. Diese erstellen zuerst eine Bohrung und entgraten das Werkstück im gleichen Arbeitsgang auf beiden Seiten. Als Folge erhält der Kunde in kürzester Zeit fertig bearbeitete Bohrungen ohne aufwändigen Werkzeugwechsel oder ein zeitintensives Umspannen des Werkstückes. Der Zuhörer der Präsentation erfährt, welche Kombinationsmöglichkeiten bestehen, welche Vorteile die Neuentwicklungen von Heule bieten und wie diese Lösungen auf seine individuelle Anwendung angepasst werden können.
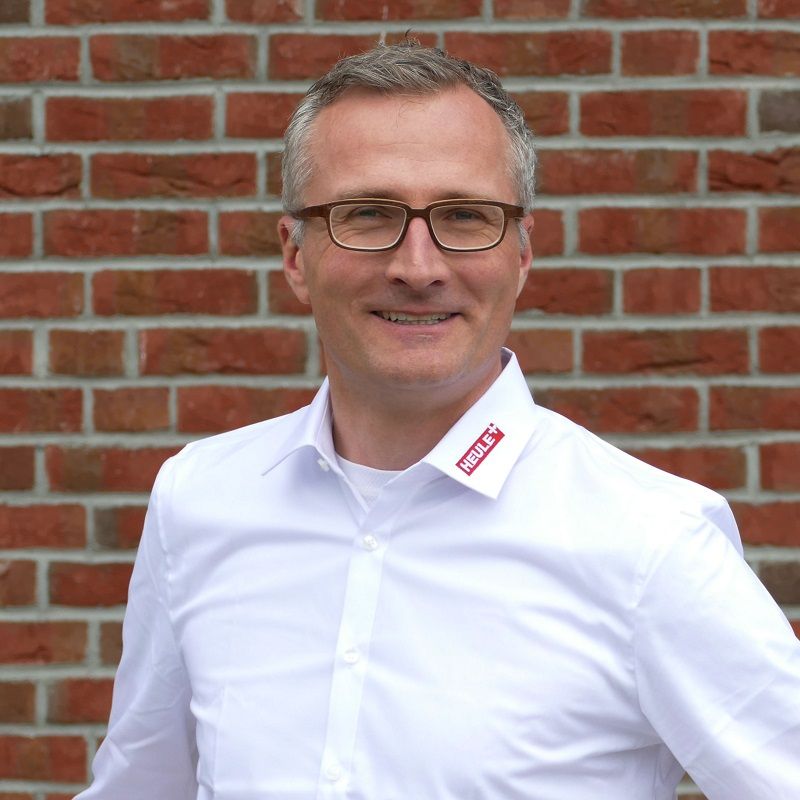
HEULE Werkzeug
11:40 - 12:00
Gezielt gekühlt - genial gefertigt: Optimierte Freiflächenkühlung verbessert Zerspanungsprozess von Superlegierungen
mehr zum Vortrag erfahren
Bei der Bearbeitung von hochwarmfesten Materialien wie Titan und diversen Superlegierungen kommt es vor allem auf zwei Dinge an: Hochwertige Werkzeuge sowie eine zielgerichtete Kühlung – zur Temperaturkontrolle und zum Standzeitenschutz der Werkzeuge. Mit dem additiv gefertigten Wendeplattenfräser der Serie MaxiMill – 211-DC gelang CERATIZIT eine hybride Werkzeuglösung, die eine ideale Kühlung an der Freifläche gewährleistet und den Zerpanprozess merklich verbessert. Im Vergleich zu Werkzeugen mit herkömmlicher Kühlstrategie bei identischen Einsatzparametern sind mit dem MaxiMill – 211-DC bis zu 60 % höhere Standzeiten möglich.
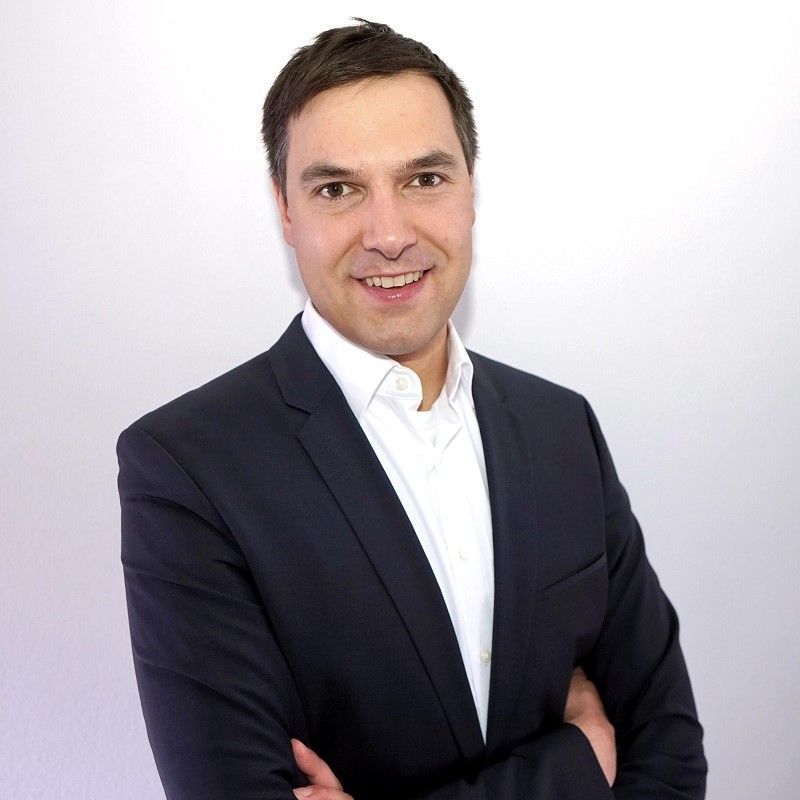
Ceratizit
12:00 - 12:20
Der virtuelle Maschinenbediener: Paradigmenwechsel in der Präzisionszerspanung
mehr zum Vortrag erfahren
In Präzisionsanwendungen wie der Metallzerspanung werden sprunghafte Produktivitätsgewinne derzeit durch zwei wesentliche Faktoren erschwert: Einerseits treibt die organisatorische und räumliche Entkopplung von Produktions- und Qualitätssicherungsprozess die Herstellkosten, sie bindet qualifiziertes Personal und ist geprägt von geringen Automatisierungsgraden. Andererseits steigen durch erhöhte Genauigkeitsanforderungen und wechselnde Umgebungseinflüsse die Aufwände für das Erreichen und dauerhafte Absichern der Prozessfähigkeit.
In diesem Vortrag zeigen wir, welche OEE-Steigerungen sich durch Kombination physischer und sog. virtueller Messtechnik erstaunlich leicht erschließen lassen. Dafür nutzen wir hochfrequente Datenströme aus maschinenintegrierten Sensoren, sowie Prozess- und Umweltdaten, um die Prüfmerkmale mithilfe etablierter Prozesskraftmodelle und einer Zerspanungssimulation schon während der Fertigung präzise vorhersagen zu können. Bei erkannten Prozesskraftanomalien oder Modelldrift kann die physische Sensorik die virtuelle Sensorik jederzeit rekalibrieren und rückführbar machen. Die latenzminimale 100%-Überwachung der Bauteilqualität ermöglicht die Implementierung eines maschinenintegrierten Regelkreises, in dem die Soll-Ist-Abweichungen kontinuierlich auf regelbare Prozessparameter abgebildet und diese dann unmittelbar über die Maschinensteuerung angewendet werden. Vorzugsweise erfolgt mittels einer zusätzlich aufmodulierten minimalen Systemanregung eine Parameterraumexploration, die mit jedem produzierten Werkstück das Prozessverständnis vertieft und insbesondere Areale weitgehend stabiler Parameterkonstellationen identifizieren kann. Konsequent angewendet lassen sich damit sogar Präzisionsanforderungen bedienen, die aus Sicht der Werkzeugmaschinen und schwankenden Produktionsbedingungen eigentlich nicht wirtschaftlich abbildbar sein dürften.
Die vorgestellte Lösung eignet sich besonders für qualitäts- und/oder kapazitätsbeschränkte Unternehmen, die ihre Gutteilausbeute sprunghaft erhöhen wollen, ohne dafür zusätzliche Investitionen in Anlagen und Personal tätigen zu müssen. Anhand konkreter Beispiele von der Unikat- bis zur Großserienfertigung zeigen wir, warum sich die Einführung der Lösung bereits im ersten Jahr rentiert.
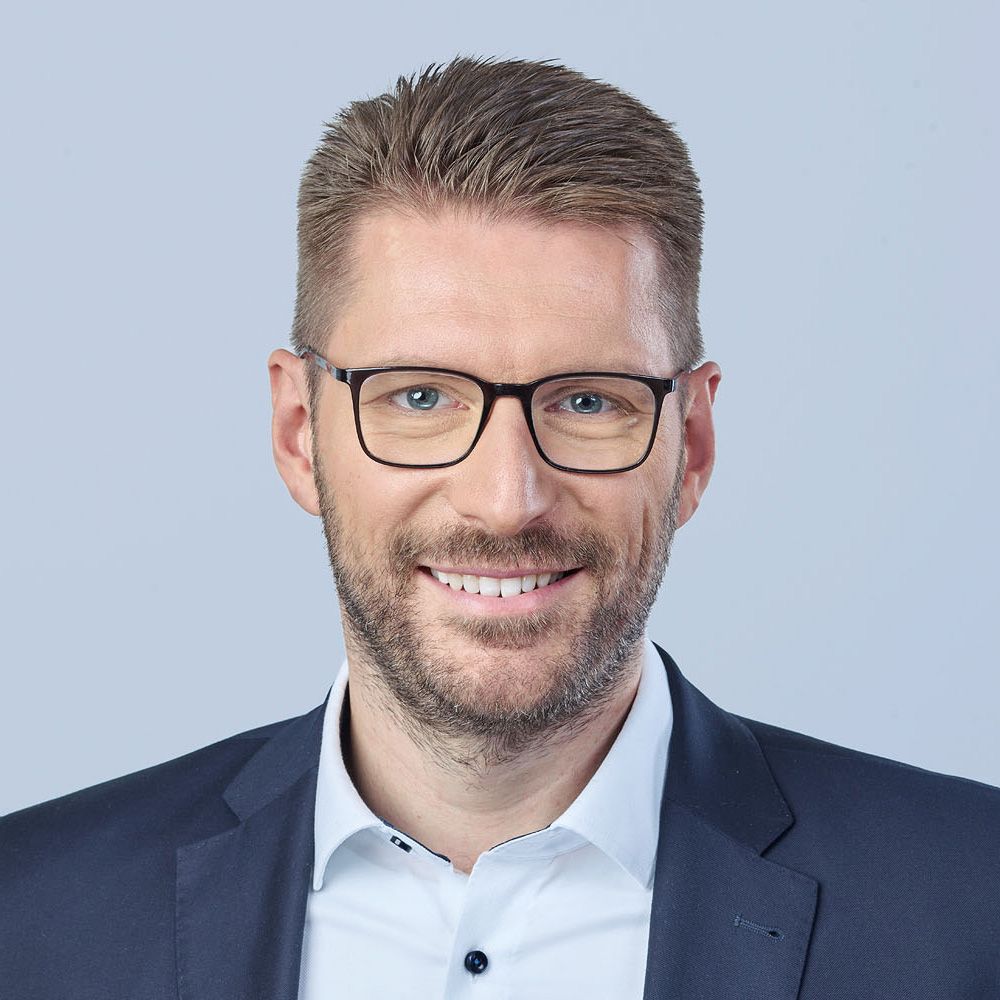
ZEISS Digital Innovation
12:20 - 13:20
Mittagspause
Möglichkeit zum Besuch der Ausstellung
13:20 - 13:30
Welcome back - Anmoderation der Nachmittag-Sessions
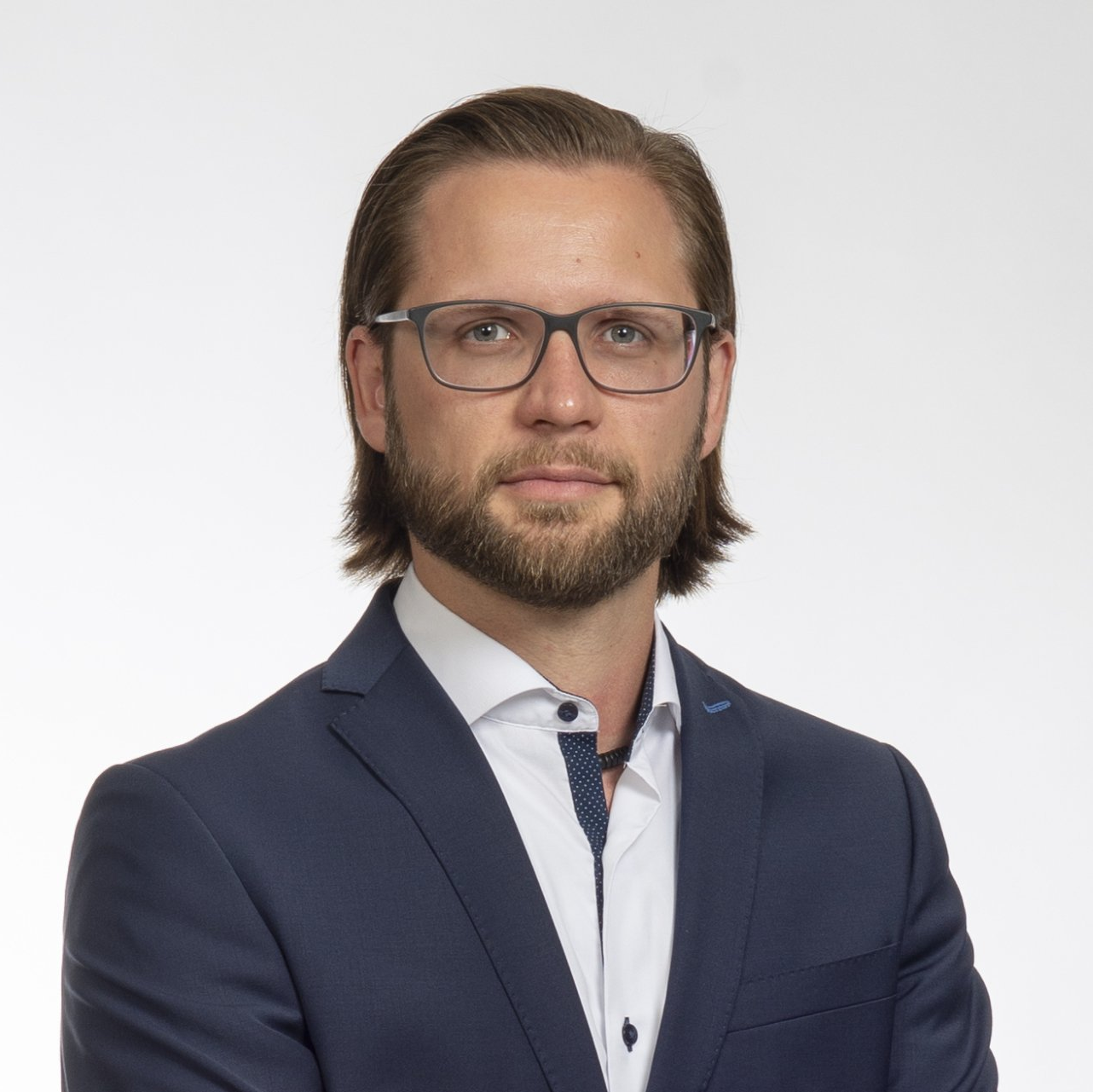
Chefredakteur MaschinenMarkt | Vogel Communications Group
13:30 - 14:00
Keynote-Vortrag
Kunden und Mitarbeiter mit Social Media gewinnen – Wie 110 Millionen Aufrufe mein Geschäft veränderten
mehr zum Vortrag erfahren
Social Media ist doch nur etwas für Influencer, oder? Das dachte ich auch, es stimmt aber nicht.
In meinem Vortrag erkläre ich, wie ich als Vollblut-Zerspaner mit Social Media in nur elf Monaten über 150.000 Follower gewann. Dass eine große Reichweite neue Kunden und Mitarbeiter anzieht, ist jedem klar. Und wie bekommt man diese Reichweite? Genau das erkläre ich beim
Wissensforum Zerspanung. Egal, ob Sie Kleinunternehmer sind oder einen Konzern vertreten, die Vorgehensweise ist für jeden umsetzbar.
14:00 - 14:20
SAUTER SolidPro®: Effiziente Automatisierung des Werkzeugwechsels bei Drehmaschinen – Potenziale und Anwendungsmöglichkeiten
mehr zum Vortrag erfahren
Der Werkzeugwechsel in Drehmaschinen stellt in der Fertigung eine zentrale Herausforderung dar. Während bei Fräsmaschinen automatische Werkzeugwechselsysteme (ATC) weit verbreitet sind, war diese Automatisierung bei Drehmaschinen bisher nicht vollständig möglich.
Der Fachvortrag beleuchtet die innovative Lösung von SAUTER FEINMECHANIK aus Metzingen: das SolidPro®-System. Mit diesem Schnellwechselsystem ist erstmals ein vollautomatisierter Werkzeugwechsel direkt am Revolver möglich, was zu deutlichen Verbesserungen bei Rüstzeiten, Effizienz und Flexibilität führt.
Im Vortrag wird zunächst die technische Funktionsweise von SAUTER SolidPro® vorgestellt, einschließlich der modularen Aufrüstungsmöglichkeiten von einem kostengünstigen Spannzangen-System hin zu einem flexiblen 2-in-1-System mit Adapterwechsel. Darüber hinaus werden die Auswirkungen von SAUTER SolidPro® auf die Automatisierung von Fertigungsprozessen aufgezeigt.
Der Vortrag bietet somit nicht nur einen technischen Einblick in die Innovationen hinter SolidPro®, sondern verdeutlicht auch den praktischen Nutzen und die Zukunftsperspektiven für Unternehmen, die ihre Drehmaschinen effizienter gestalten wollen.
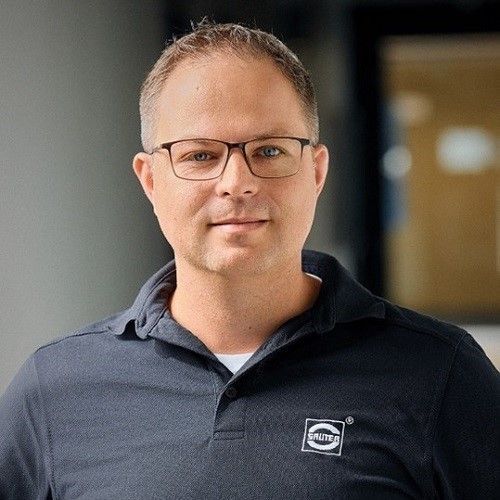
Sauter Feinmechanik
14:20 - 14:40
Keep Cool! – Effizienzpotenziale in der Prozess- und Werkzeugmaschinenkühlung
mehr zum Vortrag erfahren
Thermische Belastungen von Bearbeitungsprozessen stellen einen signifikanten Einflussparameter auf Standzeiten, Produktivität und Prozessfähigkeit dar. Während die Aufgabe von Kühlschmierstrategien (KSS) darin besteht, Wärme aus der Prozess¬zone abzuführen, übernimmt die Maschinenkühlung die Kompensation thermischer Einflüsse auf die Maschinenstruktur. Obwohl der erforderliche Energiebedarf für die KSS und die Maschinenkühlung insbesondere bei der Bearbeitung schwer zerspanbarer Materialien bis zu 75% der Leistungsaufnahme der Maschine betragen kann, sind Prozess- und Maschinenkühlung häufig überdimensioniert. Zur Erschließung dieses Effizienzpotenzials können existierende Daten aus dem CAM-System und der Maschinensteuerung genutzt werden.
Der geplante Vortrag skizziert zunächst den Status Quo in Bezug auf Prozess- und Maschinenkühlung. Zweitens wird erläutert, wie der Zugriff auf Steuerungs- und Regelungsdaten mit kommerziellen Softwarekomponenten möglich ist und diese auf individuelle Anforderungen bspw. Abtastraten abgestimmt werden können.
Anschließend werden die beiden Anwendungsfälle Maschinen- und Prozesskühlung detailliert entwickelt. Basis einer effizienten Maschinenkühlung ist ein Simulations¬modell, das sowohl die Wärmequellen der Maschine und den Wärmetransfer als auch das Verhalten des Kühlaggregates vorausschauend abbildet. Weiterhin wird eine prädiktive Regelung für die Prozess- und Maschinenkühlung entwickelt und umgesetzt.
Als weiteren Anwendungsfall skizziert der Vortrag zunächst verschiedene Alternativen zur Überflutungs-/Hochdruck-Prozesskühlung wie die Minimalmengenschmierung (MMS), die kryogene, CO2-basierte Kühlung oder die kryogene MMS. Anschließend wird die Nutzung digitaler Steuerungs- und Regelungsdaten für die Optimierung der KSS dargestellt. Der Vortrag schließt mit einer Zusammenfassung und Handlungsempfehlungen für Anwender, Maschinen- und Werkzeughersteller.
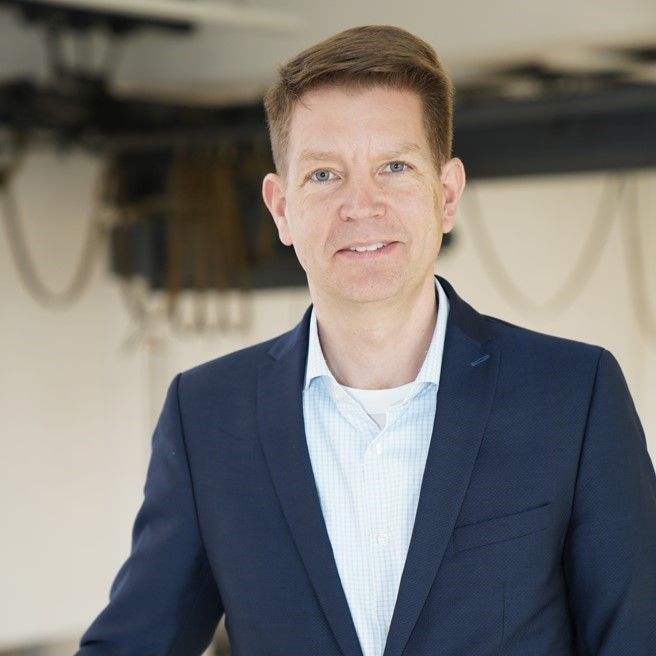
FAU Erlangen-Nürnberg
14:40 - 15:30
Parallele Workshops
Workshop-Raum 1
Hochgeschwindigkeitsfräsen mit superkritischer CO2 Kühlung (Dauer: 50 min)
mehr zum Vortrag erfahren
Kohlendioxid (CO2) wird oberhalb seines kritischen Drucks und seiner kritischen Temperatur überkritisch (Pc = 73,8 bar und Tc = 31.1 ◦C). Überkritisches CO2 sorgt für die Schmierung und ist außerdem in der Lage, die Mindestmengenschmierung (MMS), welche seinem Kühlmedium zugesetzt wird, vollständig zu lösen. Sc-CO2-Kühlmittel als neuartige „Sub-Zero“-Kühlmethode gilt als grüne Kühl- und Schmiertechnologie. Sie kann Vorteile bei der Bearbeitungsleistung bieten, wie z. B. eine erhöhte Materialabtragsrate (MRR) und Werkzeugstandzeit sowie eine verbesserte Oberflächenintegrität und eine reduzierte Gratbildung beim Hochgeschwindigkeitsfräsen.
Experimentellen Untersuchungen auf einer Mill S400 U (GF Machining Solutions) mit einem Coolant Fusion Sc-CO2 Kühlsystem zeigten, dass das Sc-CO2-Fräsen zu einer erhöhten Werkzeugstandzeit, deutlich geringeren Schnittkräften (bis zu 50 %), eine erhöhte Oberflächenmikrohärte (bis zu 30 %) und einer reduzierten Oberflächenrauheit (bis zu 50 %) im Vergleich zum Fräsen mit wasserbasiertem Kühlschmierstoff bei der Bearbeitung von Titan Grade 5 (Ti6Al4V) führte. Bei der Zerspanung von Ultrahochmolekularem Polyethylen (UHMWPE), welches ein in der medizinischen Orthopädie häufig verwendetes Material darstellt und dessen haltbare, reibungsarme Oberfläche als Spacer für Knie-, Hüft- und Schulterimplantate verwendet wird, konnte durch die Sc-CO2 Kühlung eine deutliche Reduktion der Gratbildung und eine Steigerung der Oberflächenqualität im Vergleich zur Luftkühlung erreicht werden. Dies deutet darauf hin, dass ein manuelles Entgraten stark reduziert oder sogar komplett überflüssig machen könnte.
Außerdem verringerte die Verwendung von Sc-CO2 + MMS-Kühlmittel auch die Verunreinigung der bearbeiteten Oberfläche, was eine Restverschmutzung nahezu ausschließt.
Um diesen Prozess unter optimalen Bedingungen realisieren zu können, bedarf es einer angepassten Werkzeugauslegung, Parameterwahl und Bearbeitungsstrategie.
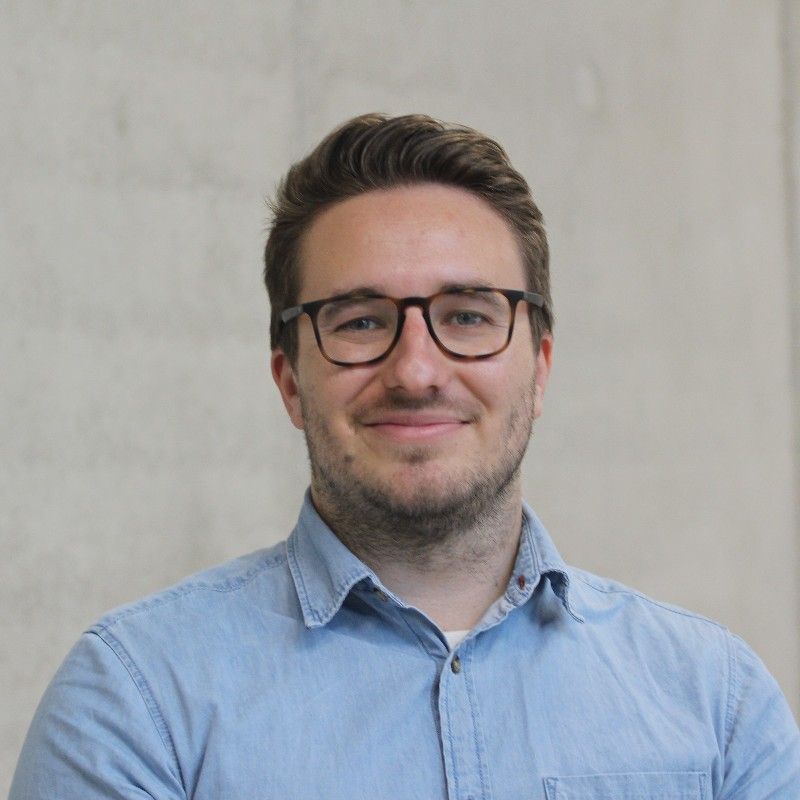
Hochschule Furtwangen
Workshop-Raum 2
Modulare Werkzeugkonzepte: Von der Bohrungsfeinstbearbeitung zum High-Speed PKD-Planfräsen (Dauer: 20 min)
mehr zum Vortrag erfahren
Modulare Werkzeugkonzepte gewinnen in der heutigen Zeit, in der Energiekosten steigen und Ressourcen immer knapper werden, mehr und mehr an Bedeutung. Die URMA-Interpretation solcher Konzepte ist die Kombination aus flexibel einsetzbaren, wiederverwendbaren, hochpräzisen Werkzeugträgern und der speziell auf die Bearbeitungsstrategie des Kunden abgestimmten Präzisions-Wechselkopfschneiden.
In diesem Vortrag wird an Hand von Applikationsbeispielen gezeigt, wie durch die Auswahl geeigneter Hartstoffe, der optimalen Auslegung von Schneidengeometrien und den Einsatz eigens entwickelter PVD-Beschichtungen, modulare Werkzeugkonzepte für die Bohrungs-Feinstbearbeitung bis hin zur Highspeed-Aluminiumbearbeitung entwickelt werden, immer mit dem Fokus auf minimalen Einsatz von Verschleisskomponenten und maximale Prozesssicherheit.
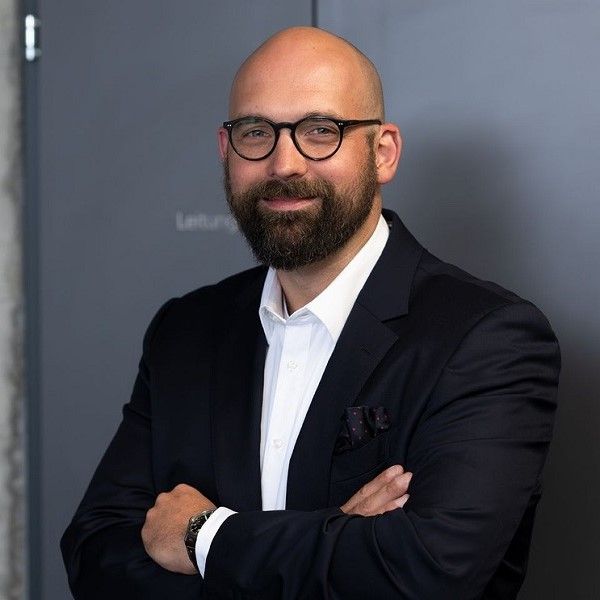
URMA AG
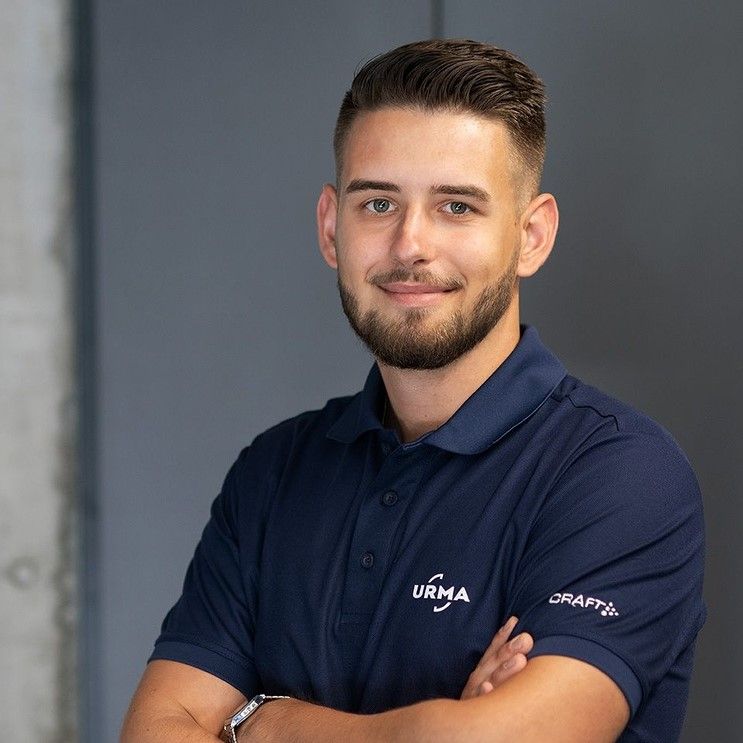
URMA AG
Referentenwechsel
3D-gelaserte Spanformgeometrien für eine bessere Spankontrolle (Dauer: 20 min)
mehr zum Vortrag erfahren
Eine optimale Spankontrolle zu gewährleisten, ist vor allem im Bereich der Kleinteile- und Mikrobearbeitung eine Herausforderung. Gleichzeitig ist eine effektive Spankontrolle unerlässlich für den Erfolg der Bearbeitung: sie verringert nicht nur den Werkzeugverschließ, sondern beeinflusst auch maßgeblich die Prozesssicherheit. Die Werkzeughersteller bieten heute vorwiegend Werkzeuge mit geschliffenen oder gesinterten Spanformgeometrien an, um die Späne zu brechen, zu formen oder in eine bestimmte Richtung zu lenken.
Allerdings sind die Prozessparameter jeder Bearbeitung höchst individuell, sodass es keine allgemeingültige Strategie für eine erfolgreiche Spankontrolle gibt. Das optimale Design einer gelaserten Spanformgeometrie wird anhand der Prozessparameter (Schnittgeschwindigkeit, Vorschub, Schnitttiefe, etc.) gemeinsam mit dem Kunden entwickelt und sorgt so u.a. in kleinen Innendurchmessern, bei hohen Schnittgeschwindigkeiten mit hohem Wärmeeintrag, hohen Formtiefen oder langspanenden Werkstoffen für optimale Ergebnisse.
Individuell designte, 3D-gelaserte Spanformgeometrien sind die effektivste und wirtschaftlichste Lösung für eine optimale Spankontrolle. In diesem Vortrag geht es daher vor allem um die Vorteile, die der Einsatz von Lasertechnik für die Spankontrolle bietet und welche Mehrwerte für Fertigungsbetriebe konkret in der Praxis dadurch entstehen. Veranschaulicht wird das unter anderem durch beispielhafte Anwendungsszenarien.
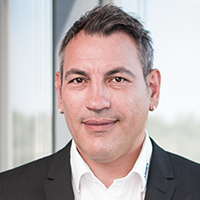
SIMTEK Präzisionswerkzeuge
15:30 - 15:50
Kaffee- & Snackpause
Möglichkeit zum Besuch der Ausstellung
15:50 - 16:10
Kühlschmierstoffe: Mineralölbasierte Emulsionen vs. Synthetische Lösungen – Vor- und Nachteile, Arbeitssicherheit und Entwicklungstrends
mehr zum Vortrag erfahren
In der Metallverarbeitungsindustrie spielen Kühlschmierstoffe (KSS) eine zentrale Rolle, da sie die Werkzeuglebensdauer verlängern, die Bearbeitungszeiten verkürzen und die Oberflächenqualität verbessern. Angesichts wachsender Anforderungen an Umweltschutz und Arbeitssicherheit steht die Wahl zwischen traditionellen mineralölhaltigen und vollsynthetischen KSS zunehmend im Fokus.
Mineralölbasierte Emulsionen bieten hervorragende Kühlung und sind kosteneffizient, erfordern jedoch regelmäßige Wartung aufgrund mikrobiellen Befalls. Vollsynthetische Lösungen überzeugen durch ihre lange Haltbarkeit und geringe Biozidbelastung, sind jedoch in der Anschaffung teurer und können mit bestimmten Materialien inkompatibel sein. Nicht-wassermischbare, mineralölhaltige KSS zeichnen sich durch ihre überlegene Schmierwirkung aus, sind aber weniger effektiv in der Wärmeabfuhr.
Die Wahl des optimalen KSS hängt von den spezifischen Anforderungen der Anwendung ab. Zunehmende regulatorische Anforderungen und das Streben nach Nachhaltigkeit fördern die Entwicklung umweltfreundlicherer und sicherer Kühlschmierstoffe, die sowohl die Effizienz als auch den Schutz von Umwelt und Gesundheit verbessern.
In unserem Vortrag werden wir alle Arten von KSS im Detail betrachten, ihre Vor- und Nachteile analysieren und aufzeigen, welche Entwicklungen in der Zukunft zu erwarten sind. Dabei legen wir besonderen Wert auf die neuesten technologischen Fortschritte und die Auswirkungen auf Umwelt und Arbeitssicherheit.
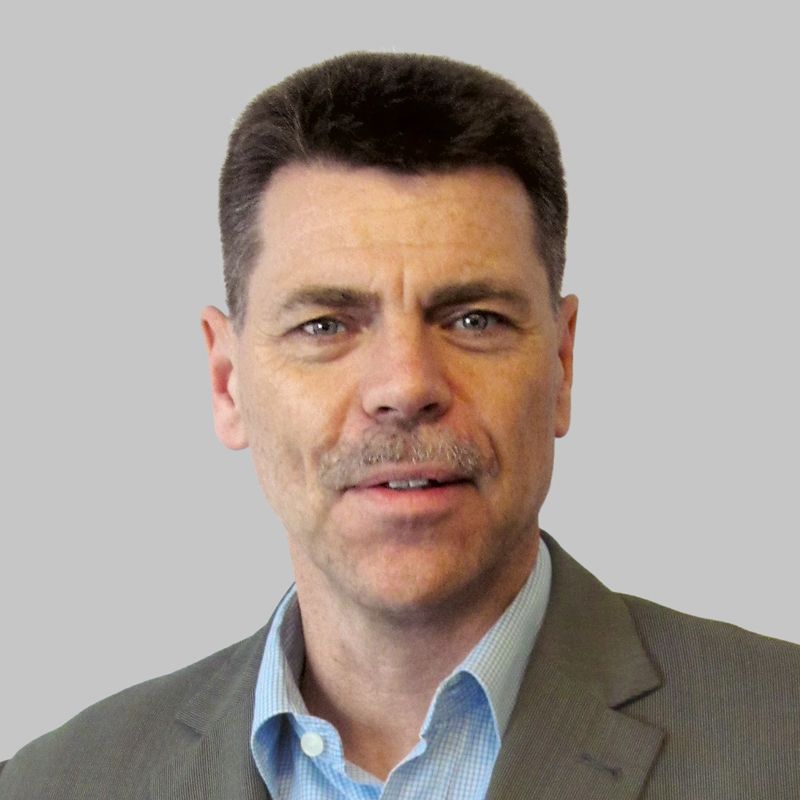
Castrol
16:10 - 16:30
Wirtschaftliche Wiederaufbereitung von Präzisionsbohrwerkzeugen entlang der gesamten Prozesskette
mehr zum Vortrag erfahren
Um Präzisionswerkzeuge wirtschaftlich ohne Nachteile in Bezug auf die Produktionskosten wiederaufbereiten zu können, müssen technologisch und wirtschaftlich nutzbare Kombinationen aus bewährten und neuen Entschichtungs-, Reinigungs- und Präparationsprozessen identifiziert und in die erforderlichen Abfolgen des Nachschleifens und Nachbeschichtens integriert werden.
Hierfür werden anhand der Analyse des Bohrens schwer zerspanbarer Materialien mit wiederaufbereiteten Werkzeugen verschiedene Trends und Herausforderungen für den wirtschaftlichen Einsatz wiederaufbereiteter Bohrwerkzeuge dargestellt. Dabei erfolgt die Optimierung von Technologien für eine effektive Prozesskettengestaltung inkl. Schneidkantenmikrogeometrie vor und nach der Beschichtung unter Berücksichtigung grundlegender Wirkzusammenhänge der Entschichtungs-, der Reinigungs- und Beschichtungstechnologie.
16:30
Summary & Abschlussmoderation
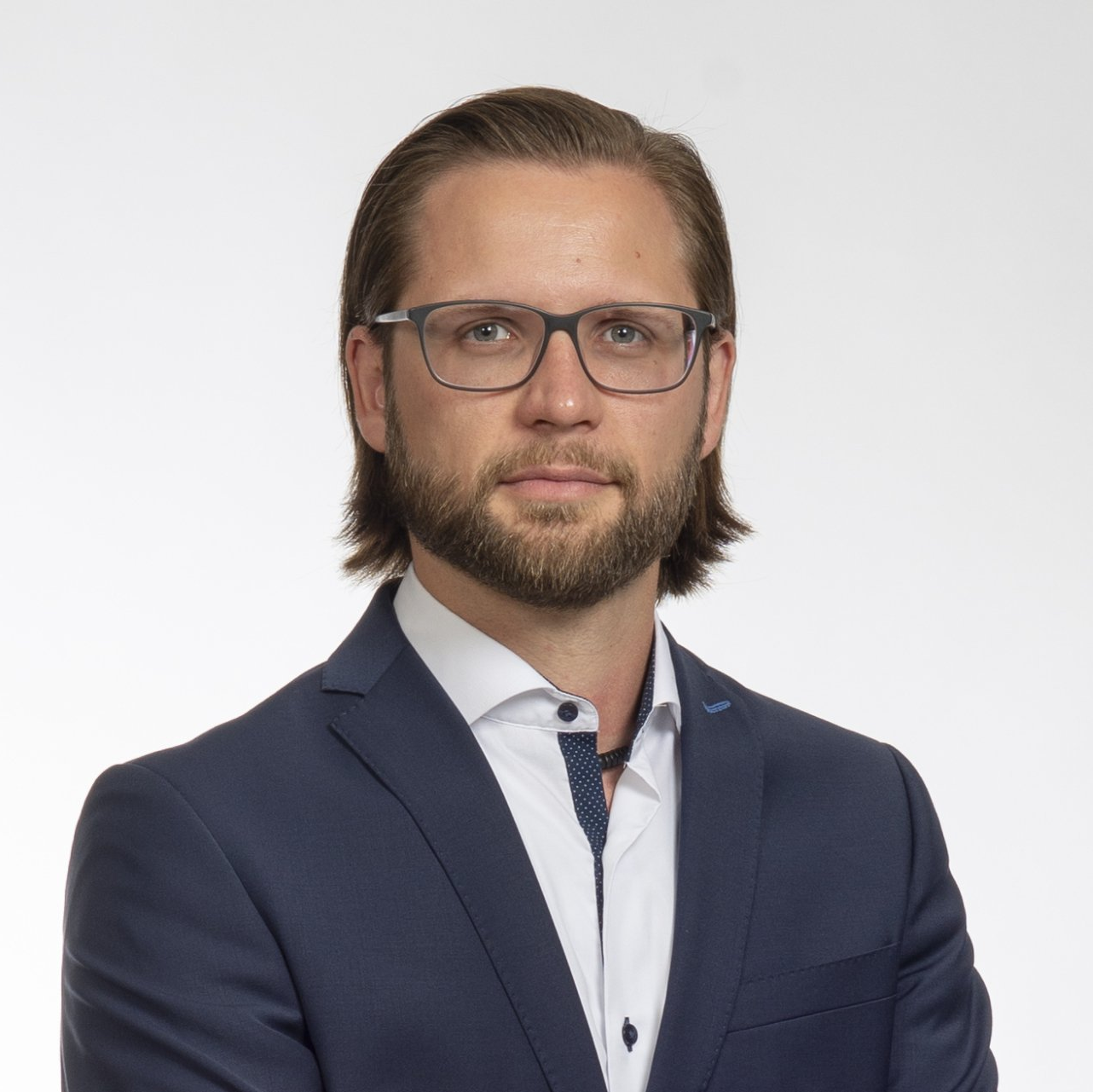
Chefredakteur MaschinenMarkt | Vogel Communications Group